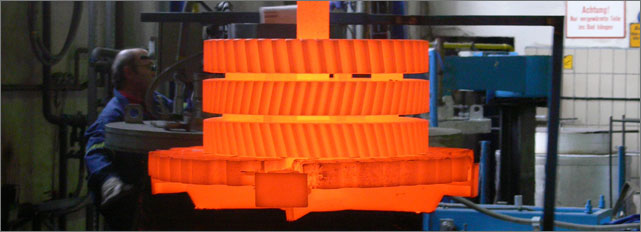
Einsatzhärten
Einsatzhärten für hohe Randschichthärte
Einsatzhärten erzeugt einen harten, verschleißfesten Randbereich und ein zäher Kern bei Stahlbauteilen und Werkstücken.
Einsatzhärten: Aufkohlen, Härten, Anlassen
Unter Einsatzhärten versteht man:
- Aufkohlen,
- Härten und
- Anlassen
eines Werkstücks aus Stahl.
Stähle, die wegen ihres geringen Kohlenstoffgehalts nicht oder nur schlecht zu härten sind, werden durch Aufkohlen soweit mit Kohlenstoff angereichert, dass eine Härtung im Randbereich möglich wird.
Werkstoffe, Härtetiefe und Prozesstemperatur
Typische Werkstoffe zum Einsatzhärten sind z.B.:
- 16MnCr5 (Werkstoff-Nr.: 1.7131)
- 20MnCr5 (Werkstoff-Nr.: 1.7147)
- 18CrNiMo7-6 (Werkstoff-Nr.: 1.6587)
Die Diffusion des Kohlenstoffs erfolgt durch kohlenstoffabgebende Gase oder Salze von der angereicherten Oberfläche zum Kern. Gängige Härtetiefen (CHD) liegen beim Einsatzhärten zwischen ca. 0,3 und 3 mm. Die Prozesstemperatur beim Aufkohlen liegt üblicherweise zwischen 880°C und 950°C.
Zur Realisierung der gewünschten Ergebnisse beim Einsatzhärten in Bezug auf Härte, Härtetiefe und Verzug müssen viele Faktoren aufeinander abgestimmt werden, wie z.B.:
- Werkstoff
- Bauteilgeometrie
- Eigenspannungszustände der Bauteile
- Chargierung der Bauteile
- Prozessführung
- Temperatur
- Haltedauer
- Gaszusammensetzung
- Abkühlmedium / Abkühlgeschwindigkeit
Partielles Aufkohlen
Anwendungsbezogen kann es nötig sein, nur bestimmte Bereiche eines Werkstücks aufzukohlen (partielles Aufkohlen). Bereiche des Werkstücks, die nicht aufgekohlt werden sollen, müssen hierzu mit einer speziellen Paste abgedeckt werden.
Nach Aufkohlen: Härtung der Bauteile
Im Anschluss an die Aufkohlung erfolgt die Härtung der Bauteile. Durch den Kohlenstoffverlauf in der Randschicht ergibt sich beim Abschrecken ein Härtetiefenverlauf mit der entsprechenden Oberflächenhärte und Einsatzhärtungstiefe. Die Randhärte eines einsatzgehärteten Stahls wird überwiegend vom Randkohlenstoffgehalt bestimmt. Die bei der Aufkohlung eingestellte Aufkohlungstiefe, die Legierungszusammensetzung des verwendeten Stahls und die Abschreckintensität des verwendeten Abschreckmediums, z.B. Salzbad-Abschreckung, beeinflussen die Einsatzhärtungstiefe. Im Anschluss an das Härten der Bauteile wird umgehend bei ca. 160 – 220°C angelassen, um der zunächst extrem harten Randschicht wieder mehr Duktilität zu geben.
Vorteile und Nachteile des Einsatzhärtens
Vorteile:
- Variable Einsatzhärtetiefen (CHD)
- Harter und verschleißfester Rand, zäher Kern
- Deutliche Steigerung der Biegewechselfestigkeit und der Dauerfestigkeit
- Partielle Oberflächenhärtung möglich
Nachteile:
- Nacharbeit erforderlich (Schleifzugabe berücksichtigen)
- ca.180°C Entspannungstemperatur
- höhere Umgebungstemperaturen im Einsatz nicht möglich
Prüfprotokoll nach DIN 6773
Auf Anfrage erstellt Ihnen die Härterei TANDLER ein Prüfprotokoll über die Härtemessung nach DIN 6773.
Lassen Sie sich kostenlos beraten!
Sie haben Fragen zu unseren Produkten und Leistungen und wünschen dazu eine kostenlose Beratung für Ihre individuelle Aufgabenstellung?